Footprint Optimierung
Ausgangssituation.
Global tätiger Automobilzulieferer. Produkt mit teilweise über 450 Varianten. Unternehmensgruppe mit 16 weltweiten Standorten.
Der Produktionsschritt vor der finalen Montage war bislang nur über mehrere parallele Batch-Behandlungsanlagen möglich. Daher kein One-piece-flow möglich. Ungewöhnlich hoher Produktions-Footprint. Umfangreiche Arbeitsvorbereitung erforderlich. Sehr umfangreiche Logistik.
Ziel 1: Optimierung des Produktions-Footprint: gefordert war eine pragmatische, szenariobasierte Lösung, die die Auswirkungen auf u.a. Transport, Flächeneffizienz, Arbeitskräfte, Wartbarkeit berücksichtigt.
Ziel 2: Erreichen eines One-Piece-Flow als möglicher Benefit aus den Vorabgesprächen mit HME.
Lösungsansatz.
- Analyse der Ist-Situation
- Layout- und Anlagenplanung, Konzeption der optimierten Lösung
- Prototyp zur Pre-Erstmuster-Erstellung und Freigabe
- Validierung – Reduzierung der möglichen Technologierisiken
- Begleitung der Umsetzung
Nutzen für den Kunden, Lösung & Ergebnisse.
- One-piece-flow, wesentliche Prozessvereinfachung, Umsetzung einer one-fits-all Bearbeitungsanlage für alle weltweiten Standorte. Voller Erfolg für den Kunden. Wesentliche Verkürzung der Durchlaufzeiten. One-Piece-Flow.
- Zwei Produktionsanlagen konnten in einer integriert werden. Und das für alle Standorte. Und an jedem Standort mehrfach.
- Durch die damit steigende Komplexität der Prozesse verändern sich auch die Anforderungen an die Produktions-Landschaft, deren Hauptanlagen zu Beginn unserer Zusammenarbeit primär aus individualentwickelten Lösungen bestanden hat.
Sie planen ein ähnliches Projekt? Dann sprechen Sie mich einfach an!
Fertigungsunternehmen der Hightech- sowie Automobilzulieferindustrie und des Maschinen- und Anlagenbaus vertrauen meiner langjährigen Erfahrung und meiner fundierten Expertise.
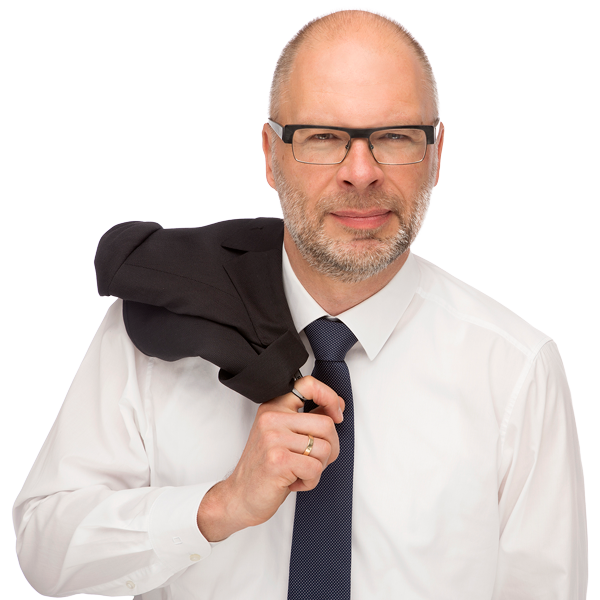